- Допълнително производство: съвместният проект с Porsche и Trumpf дава първото в света 3D принтирано бутало
- Успешно тестване в Porsche 911 GT2 RS: 200-часов тест за издръжливост на изпитателния стенд при най-тежки условия
- 3D принтираното бутало увеличава производителността и ефективността на задвижващото устройство с мощност 700 к.с.
- MAHLE специално разработва своя опит в 3D печат за приложение в областта на алтернативните устройства
Като част от сътрудничество с производителя на спортни автомобили Porsche и машиностроителната компания Trumpf, MAHLE произвежда високопроизводителни алуминиеви бутала, използващи техники за 3D печат за първи път. Буталата бяха успешно тествани на тестовия стенд на двигателя за спортния автомобил на Porsche 911 GT2 RS. Докато стандартните ковани бутала са достигнали границите на техния потенциал, може да се предположи, че мощността на двигателя Porsche от 700 к.с. ще да бъде увеличена с 30 к.с. свързано увеличаване на ефективността. MAHLE специално разработва своя опит в 3D печат, така че в бъдеще ще може да поддържа клиентите си в областта на алтернативни устройства, включително електрически, чрез бързо производство на подходящи компоненти за устройства, термично управление и мехатроника.
„Резултатите от проекта потвърждават големия потенциал на 3D печат и демонстрират специалната компетентност на MAHLE в областта на високоефективните малки и ограничени тиражи и по отношение на прототипирането и следпродажбения пазар“, казва д-р Мартин Бергер, ръководител на корпоративните изследвания и иновативен инженеринг в MAHLE.
Франк Икингер, ръководител на проекти в Porsche, коментира: „Благодарение на тясното сътрудничество на всички участващи, ние успяхме да демонстрираме потенциала на допълнително производството в нашия най-високопроизводителен спортен автомобил, Porsche 911 GT2 RS , като по този начин изчиства пътя за използването му в бъдещи модели. По отношение на технологията, това е началото на нова глава за нас, която отваря напълно нови възможности в дизайна и производството.” Steffen Rübling, мениджър на проекти в Trumpf, също вижда големи възможности за 3D печат в бъдещите производствени процеси. „Проектът илюстрира как 3D печатът може да се използва за по-нататъшно подобряване на компоненти, чийто потенциал вече е изчерпан от десетилетия на развитие. Това ще бъде от полза за много други отрасли, като например космическата и енергийната дейност.
Bionic дизайн намалява теглото на буталото и увеличава максималната скорост на двигателя
Новият процес представя възможността за прилагане на така наречения бионичен дизайн. При този подход, който имитира природни структури като човешкия скелет, материалът се добавя само в натоварени места, като структурата на буталото е адаптирана към товара. Спестява материал и има потенциала да направи 3D принтирано бутало с до 20 процента по-леко от конвенционално произвежданото, като същевременно се повишава твърдостта.
В допълнение, разработчиците на MAHLE са въвели оптимално разположена и специално оформен канал за охлаждане в близост до буталните пръстени. Този дизайн се основава на многогодишния опит на MAHLE с термичните процеси на буталото и е възможен само с помощта на 3D печат. Охлаждащият канал намалява температурното натоварване в така наречената периферия на челото, особено напрегната част на буталото, като по този начин оптимизира изгарянето и проправя пътя за по-високи максимални обороти на двигателя.
Новият производствен процес се основава на специална алуминиева сплав, разработена от MAHLE с дълга история на успешна употреба в чугунени бутала. Сплавта се атомизира във фин прах и след това се отпечатва в процес, известен като лазерно синтезиране на метал (LMF). Лазерен лъч разтопява праха до желаната дебелина на слоя, последвано от нанасяне на нов слой отгоре, като по този начин изгражда върху буталото един слой в даден момент. Използвайки този метод, специалистът по 3D печат Trumpf произвежда заготовки на буталото, съставени от приблизително 1200 слоя за около 12 часа.
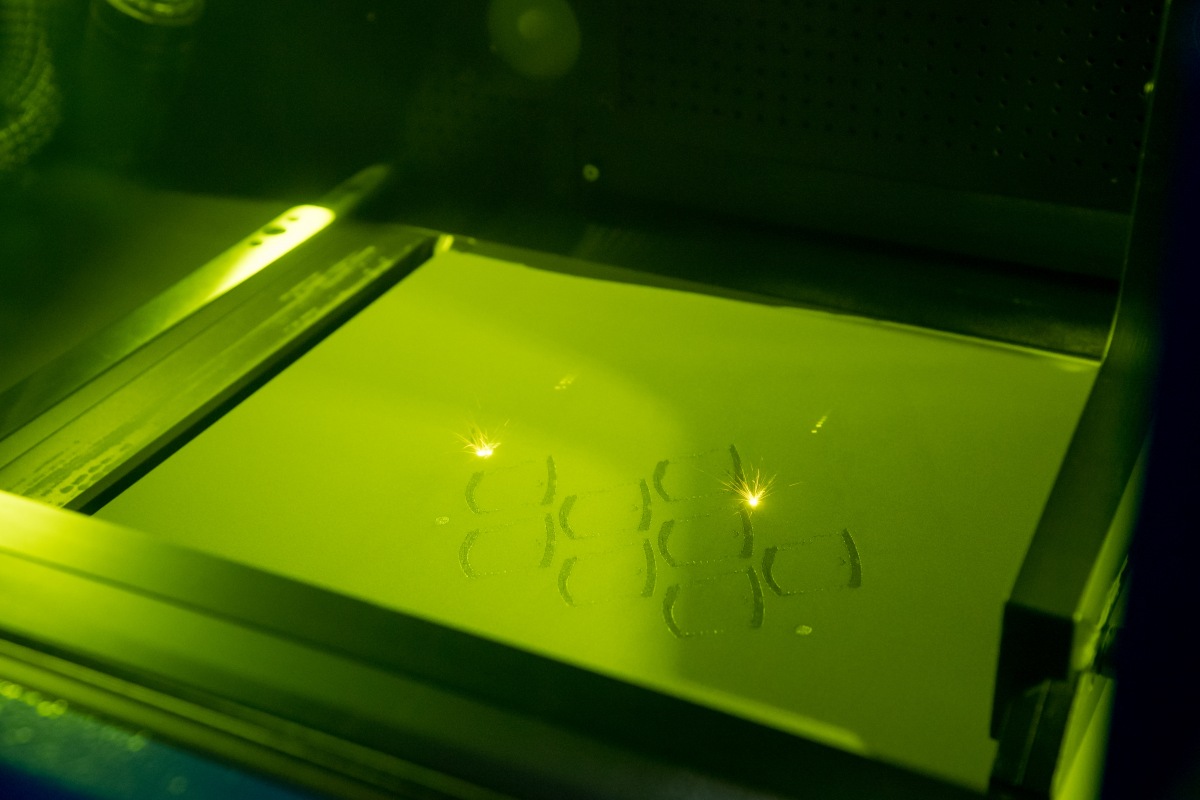
„Този проект включваше множество предизвикателства. От дизайна на буталото до спецификацията на материала и разработването на подходящи параметри, трябваше да направим много фини корекции, за да постигнем оптималния резултат “, обяснява Волкер Шал, ръководител на продуктовия дизайн в Advanced Engineering в MAHLE. „Вече не само усвоихме техническата страна на нещата, но можем и да преценим как методът може да бъде вграден в съществуващите производствени процеси.“
Високо качество, потвърдено в строг тестов цикъл
След това заготовката на буталото се завършва, измерва и тества в MAHLE и трябва да отговаря на същите строги стандарти като конвенционално произведената част. Специално внимание се обръща на полата на буталото в точката, в която тя се свързва с мотовилката – отвора за буталния болт. Тези зони се подлагат на тестове за пулсации и разрушаване на полата; По този начин инженерите на MAHLE могат да симулират натоварванията, които ще възникнат по време на бъдеща експлоатация.
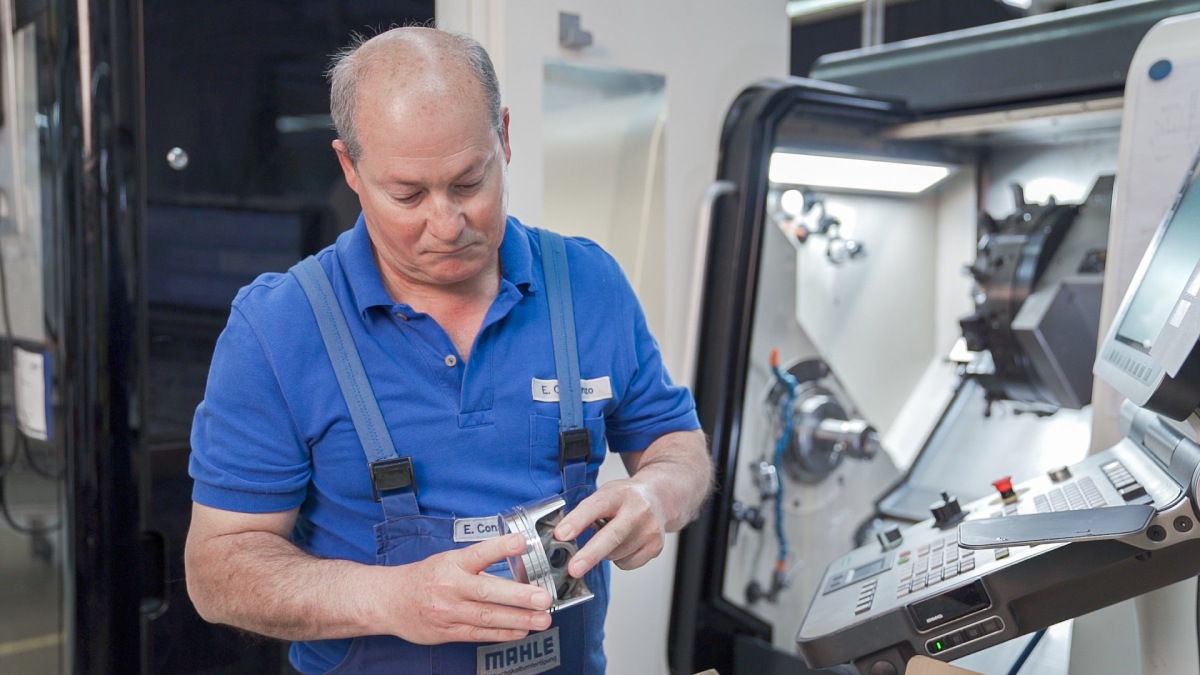
Опит: Довършителната обработка на отпечатаната заготовка изисква работа: резултатът
трябва да отговарят на строгите стандарти на MAHLE
В допълнение към провеждането на анализ на бутала, партньорът на проекта Zeiss проведе множество неразрушаващи тестове, използвайки процедури, включващи CT сканиране, 3D сканиране и микроскопия. Резултатите показват, че отпечатаното бутало постига същия висок стандарт за качество като конвенционално произведеното производствено бутало.
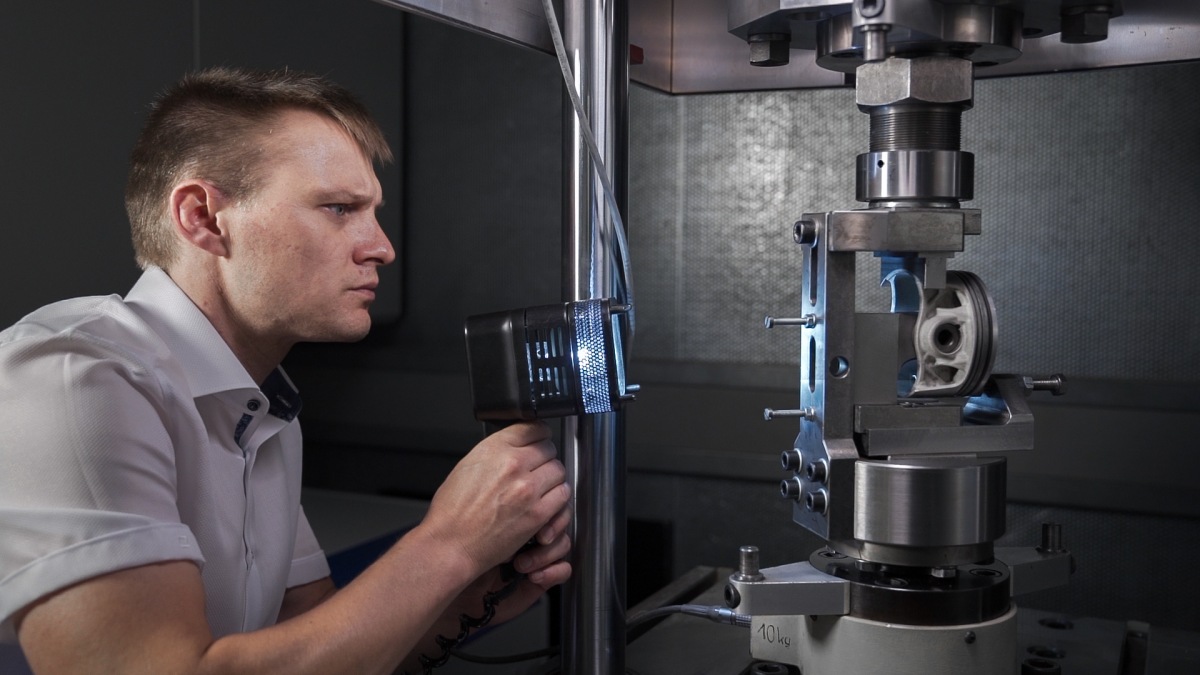
Прецизност: Стената на полата на отпечатаното бутало се тества – 100 години
опит в конструкцията на бутала гарантират перфектен резултат.
Когато стана дума за практически тестове, в двигателя на Porsche 911 GT2 RS бяха монтирани шест бутала, а задвижващият блок успешно завърши 200 часа тестове за издръжливост при най-трудните условия на изпитвателния стенд. Това включваше около 6000 километра със средна скорост 250 км / ч, включително спиране за зареждане и около 135 часа при пълно натоварване. Тестовият цикъл също включваше 25 часа моторно натоварване, т.е. симулиран режим на претоварване на превозното средство.

Допълнителен въздушен охладител за още по-голяма ефективност
Доказателства за предимствата на 3D принтирането са осигурени от допълнителен охладител за въздух, отново разработен като част от съвместния проект с Porsche и Trumpf. Скрит във въздушната тръба между турбото и оригиналния охладител за въздух, този допълнителен компонент се възползва от значително по-голяма повърхност за пренос на топлина благодарение на възможностите, които се разкриват чрез 3D печат. Това позволява да се оптимизират контрола на потока и охлаждането, което води до по-хладен входящ въздух, повишаващ работата на двигателя и по-нисък разход на гориво.
MAHLE стратегически разширява своята компетентност в 3D печат
MAHLE развива потенциала на новите производствени процеси, като 3D печат, за по-нататъшни проекти и има за цел конкретно да разшири своята компетентност в тази област. По-краткото време за разработка и производство представлява голямо предимство. Това е особено вярно, когато става дума за нови технологии като електронната мобилност, при които са необходими компоненти за термично управление със сложни структури за осигуряване на охлаждане и климатизация в електрически превозни средства, корпуси на двигатели или трансмисии и акумулаторни системи. Други примери включват оптимизирани компоненти в периферията на двигателя, като въздушни пътища, корпуси на филтри и компоненти за управление на маслото.
Определени са и необходимите области по отношение на разработването на малки партиди и на компоненти, спряни от производство за следпродажбения пазар за стари превозни средства. Други перспективни области на приложение включват бързо създаване на прототипи, т.е. бързо изграждане на части за тестване и обратен инженеринг – възпроизвеждане на компоненти от 3D сканиране.
Коментари